One Team, One Mission – How the FAA Maintains its Fleet
By Tom Hoffmann, FAA Safety Briefing Managing Editor
Throughout this issue, we’ve explored in great detail the diverse set of missions performed by the FAA’s Flight Program Operations and their significant contribution to the safety of the National Airspace System (NAS). None of these services would be possible without the ability to properly maintain a fleet that performs such a variety of critical services in some of the most extreme conditions and challenging environments on the planet. There is a team of more than 240 people working diligently around the clock, largely behind the scenes, to keep the FAA’s fleet of nearly 40 aircraft up and running. Let’s take a closer look at this operation and some of the secrets to its success.
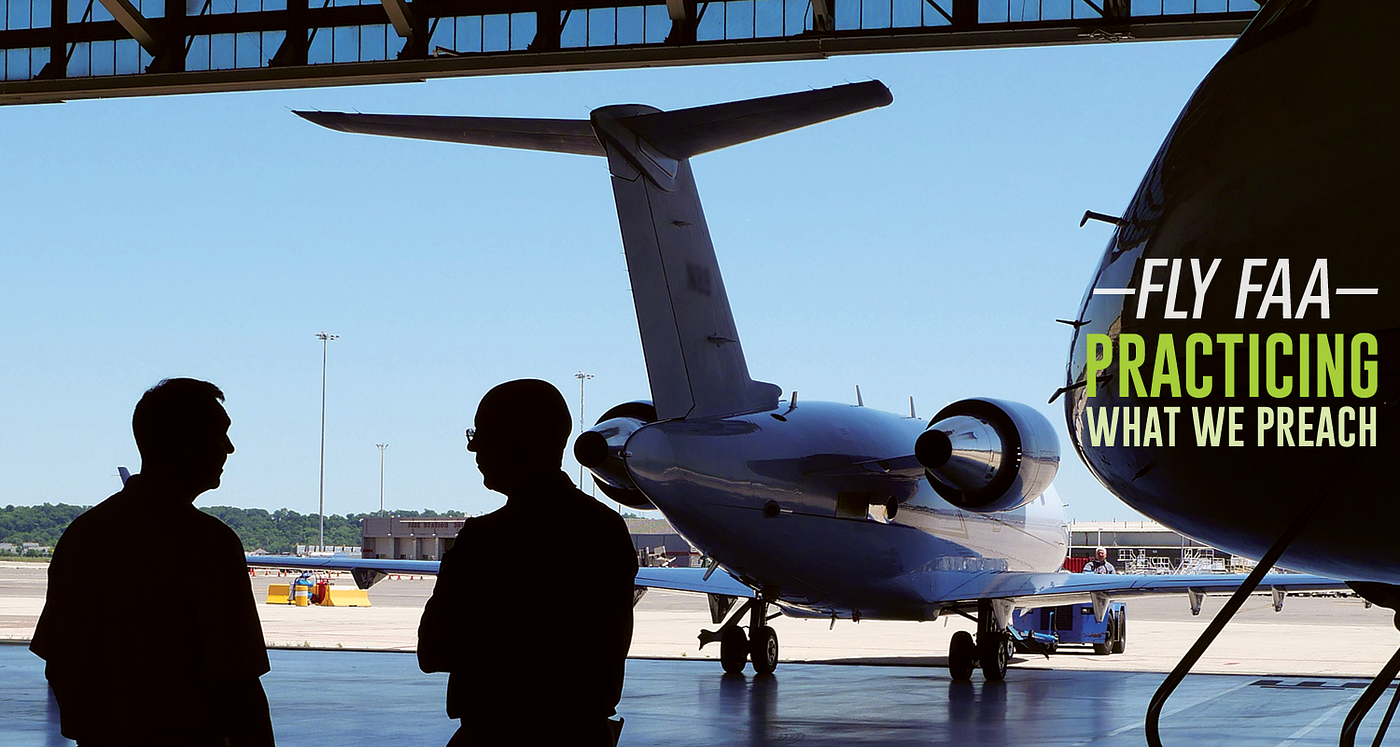
The Flight Program Operations maintenance organization is composed of two separate groups: the Maintenance Support Group and Maintenance Services Group. The former operates under the authority of a 14 CFR part 135 air operator certificate. This group includes a combination of federal and contract employees under the following units: Maintenance Control and Planning; Maintenance Program Standards; Quality Assurance; and Training and Engineering. The Maintenance Support Group creates and maintains the programs, technical data, maintenance schedule, and engineering support for the fleet.
Complementing the work of the Maintenance Support Group is the Maintenance Services Group, which operates under the authority of a 14 CFR part 145 repair station certificate. This group is located primarily at the Oklahoma City maintenance facility at the FAA’s Mike Monroney Aeronautical Center and has seven satellite stations in Anchorage, Alaska; Sacramento, Calif.; Battle Creek, Mich.; Fort Worth, Texas; Atlantic City, N.J.; Washington, D.C.; and Atlanta, Ga. There are approximately 170 aircraft technicians, a group that includes both federal and contract employees assigned across the line stations and main base facilities. They perform approximately 85% of all scheduled maintenance inspections for the fleet.
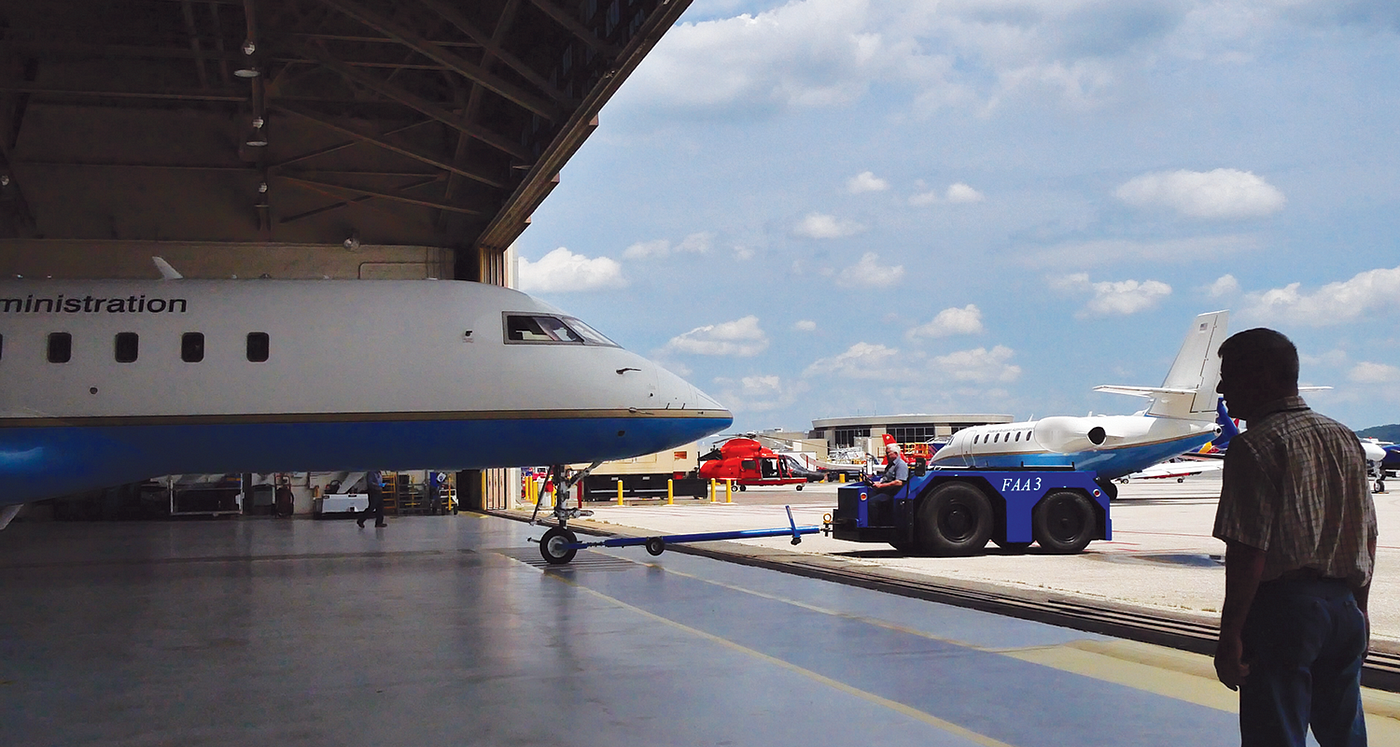
As both a certificated part 135 operator and part 145 repair station, the maintenance team is required by regulation to follow the part 135 Continuous Airworthiness Maintenance Program (CAMP) without deviation. This means that the Maintenance Services Group must perform all scheduled inspection, maintenance tasks, repairs, and modifications in accordance with the part 135 job cards, maintenance manuals, engineer orders, or other technical data.
We understand that continuous improvement is the name of the game, so no matter how good we get, we can always be better.
“As the FAA, we believe that we should set the standard for professional performance,” says Michael Bianchi, the director of maintenance for the Flight Program Operations organization. “We understand that continuous improvement is the name of the game, so no matter how good we get, we can always be better.”
To support that mantra, Bianchi implores his staff to continually ask what went well, or not so well, after every inspection.
This philosophy has proved critical to the group’s success, especially given the variety of aircraft types and the extreme conditions and circumstances under which many of the aircraft in the fleet are flown. There is also the matter of having an average 30-year fleet age, which exponentially increases the discovery rate of corrosion, fatigue cracking, and structural failures during scheduled inspections.
“The aircraft equipment and component failure rates are much higher than those of newer aircraft,” says Bianchi, “which may negatively impact our mission and our overall support of the NAS if not addressed.”
Despite these challenges, the Flight Program Operations maintenance team has shined in recent months, boasting an impressive average of 20 mission-ready aircraft per day. Bianchi credits this achievement in operational availability to a practice of yield management, where aircraft are generally not flown to zero time left before inspection.
“An 80/20 yield posture works well, which doesn’t burn up too much ‘green time’ and still allows for flexible planning,” Bianchi explains.
Further boosting the fleet’s efficiency and availability is the development of its Modular Mission System (MMS), a truly novel idea that allows aircraft to more easily transition between activities. The MMS is essentially a compact shelf rack that houses all required equipment for flight inspection, including radio receivers, a spectrum analyzer, and a computer that can quickly be swapped in and out of an aircraft depending on its mission. This is a welcome change in fleet versatility given that the existing equipment on inspection aircraft is hard-wired into the aircraft and weighs about 860 pounds. Moving forward with the MMS will allow the agency to save on several precious commodities: space, weight, time, and money.

Yet another effort to improve efficiency is the maintenance team’s planned migration to an electronic record-keeping system. This will help make maintenance operations appear in real-time and will allow for electronic logbook entries. For example, a pilot can make an electronic logbook entry for a discrepancy, which is then retrieved and handled by the appropriate technician. Maintenance control can see in real-time when this is completed and more promptly release the aircraft back to service. The same thing would occur for inspections. Electronic inspection cards will allow planners to see the status of inspections in real-time and plan accordingly to get that aircraft mission-ready as soon as possible. The FAA plans to make this transition in 2023.
Of course, training and education is a core element to any organization, especially when highly technical procedures and the potential for human error is involved. To aid with educating and supporting a positive safety culture among the maintenance crews, Bianchi has set a goal for having 100% of the group’s maintenance technicians enrolled in the FAA Safety Team’s AMT Awards Program. He aims to receive a Gold Employer Award of Excellence in the first year and is striving for the Diamond award in the near future. See Advisory Circular 65–25: Aviation Maintenance Technician Awards Program, for more information on this program that encourages AMTs to seek out recurrent training.
An advocate for thorough communication, Bianchi also develops regular PowerPoint messages that are sent to team members at all the stations across the system. Dubbed the Monthly Maintenance Message, these notices keep everyone in the loop on important personal health and safety issues, regulatory reminders, staff news, and a snapshot of the maintenance team’s scorecard (metrics) for the month. These messages will become even more far-reaching once electronic record keeping enables everyone to have their own tablet.
Managing the maintenance of a diverse fleet that flies more than 14,400 hours a year to all corners of the globe and in weather conditions across the spectrum is definitely no small feat. Thankfully, the Flight Program Operations maintenance team is up to the task by embracing ingenuity and remaining tirelessly dedicated to supporting the greater mission of improving NAS safety.
“We have a very solid team composed of great leaders and public servant aviation professionals,” says Bianchi. “They absolutely understand the importance of our noble mission to keep the flying public safe.”